
Stability Testing for Cosmetics and Personal Care Product
The purpose of stability testing is to ensure that the skincare or cosmetic products maintain their intended physical, chemical, and microbiological quality, as well as functionally and aesthetically when stored under appropriate conditions. Because the development cycle of cosmetic products is relatively short each manufacturer should design its own stability testing program such that it is economically reasonable and efficiently addresses the testing required.
Because of the wide variety of cosmetic merchandise “standards,” stability tests can't be prescribed. Manufacturers require the power to regulate trying out protocols and to construct a valid scientific basis for assessing the stability of their personal products. Thus, specific tests may be developed in order to address new or unusual technologies or to be adapted to products having extended shelf lives.
There are no authorities' requirements for stability testing out for cosmetics due to the wide variety of cosmetic merchandise. A proper manufacturer can have sound knowledge of enterprise pointers and extensive formulating revel, permitting them to alter trying out protocols and develop specific tests to assess a new or modified formulation.
As a reputed GMP certified cosmetic manufacturer India and OEM cosmetic manufacturer in India, Aadhunik Ayurveda follows robust stability protocols to meet global product standards.
What is Stability Testing?
Stability testing for cosmetics ensures product quality. Stability tests are predictive checks, geared toward assessing the ability of a product to maintain the desired physical, chemical, and microbiological properties, in addition to useful and aesthetic properties while stored and used under appropriate conditions by the consumer.
Stability tests additionally compare compatibility for market conditions wherein the product is offered and used. Market conditions encompass distribution (transportation), storage, and conditions for the duration of use.
There are three forms of stability tests.
- Physical and chemical integrity
- Microbiological stability
- Packaging stability
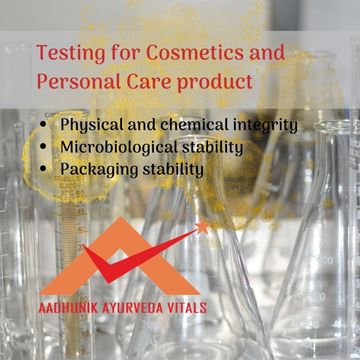
1. Physical/chemical stability test
It’s very important to figure out how the product will react or perform under common external threats like light, radiation, temperature etc. and therefore physical and chemical stability tests play a significant role in determining the same. Physical and chemical stability testing for cosmetics looks at the aesthetics (appearance, color, odor, texture) as well as the stability of the formulation itself.
Aadhunik Ayurveda, a chemical-free skincare manufacturer and private label cosmetic manufacturer India, uses these methods in its product development process.
Common stability tests include
Cycle testing: which involves cycling the product through different temperatures. Each ‘cycle’ involves placing the product at 10° for 24 hours and then placing the product at 25° (room temperature) for another 24 hours. A product is considered stable only if it passes all the three cycles.
Temperature variations: Since real time stability testing does not prove stability in the product hence high temperature testing is undertaken to establish the long term stability. If a product is stored at 55° for 3 months without issues, then it should be stable at room temperature for a period of one year.
Centrifuge trying out: when oil and water are mixed in an emulsion, there may be a tendency for the product to separate. There are ways to rule out separation like placing the product in a sheer rotating speed to stress the product with extreme movements and see if the separation occurs.
Light exposure trying out: formulas and packaging may be touchy to UV exposure and radiation. Manufacturers will expose products in transparent glass, the intended packaging, and in an opaque container to complete the formula and the intended packaging to light exposure.
Mechanical shock testing: shipping movements may damage the cosmetic products or their packaging, so vibration testing (e.g.: on a pallet shaker) can reveal any issues.
Monitoring: for all the above-mentioned tests you should monitor the colour, odour/fragrance, viscosity, pH value, and, if available, particle size uniformity and/or particle agglomeration under the microscope.
2. Microbiological Stability Tests
Microbial contaminants normally come from two exceptional stages: production and filling, and during consumer use. Contamination is after all bad be it at any stage as it creates problems leading to rancidity - affects the quality and longevity.
Routine microbiological analysis of every batch of the finished product is essential to ensure the safety of the customer and the quality of the product.
Microbiological stability tests for cosmetics include:
Screening checks- dip-slides or plate counts are used to decide whether a product is considered contaminated.
Quantitative tests- those tests determine the actual count level of bacteria, micro-organisms, and yeast in a product.
We at Aadhunik Ayurveda, a leading ayurvedic cosmetic manufacturer India, ensure stringent microbial controls from start to finish.
3. Packaging stability test
Stability testing includes packaging compatibility with the product. Packaging plays a major role in keeping the qua;ity intact of the product as product may interact with packaging material and the external environment.
Packaging won't completely defend the product or keep the product’s aesthetic characteristics (e.g. Colour, fragrance). Product components might also chemically react with the container.
Packaging stability tests for cosmetics include
Glass tests- glass is the most inert material and does not react with a cosmetic product in any way, allowing the manufacturer to determine if the problem is the formula or the package.
Weight loss tests-weight loss evaluation facilitates determining evaporation ( water loss through the container's partitions or closure gaps including lids).
Leaking tests- the packaged product is tested in various orientations to determine any issues with leaks during transport and storage.

When should stability testing for cosmetics occur?
Stability testing is essential for new formulations and for ongoing control and quality assurance. Stability testing just can not be ignored as it is must to analyze many situations and conditions:
- New prototypes
- New raw material supplier
- New production site, equipment, or, procedures
- New or modified packaging
- Scaling up production
- New regulations
Conclusion
It can advantage cosmetic manufacturers to include recurring stability testing into the lifecycle of their product making. By acquiring these vital facts about a product, manufacturers can create potent stable products at the same time without any chance of contamination and poor performance.Here at Aadhunik Ayurveda, manufacturer, a skincare products manufacturer in India and Private Label of skincare & hair care, we no longer undertake the last stage tests but we additionally check raw material to mid-production and on the final of the run, to make certain that no product we make has been contaminated at some stage in the making, filling and packaging system.
FAQ
Do all cosmetic manufacturers conduct stability testing?
Only responsible companies like Aadhunik Ayurveda, a GMP-certified cosmetic manufacturer in India, ensure full-cycle testing at every production stage. A full in-house laboratory set up is required to undertake the stability tests; hence a genuine manufacturer will always have in-house laboratory.
Can I get stability-tested products under my brand?
Yes, as a private label cosmetic manufacturer in India, we provide fully tested, branded formulations customized to your label.
What types of products can be included in a private label skincare kit for hotels and spas?
A private label skincare kit can include cleansers, exfoliators, massage oils, creams, herbal teas, and travel-sized products customized to your spa/hotel's brand and theme.
Can you help launch a monsoon skincare brand in India for spa and wellness resorts?
Yes, Aadhunik Ayurveda supports the launch monsoon skincare brand in India with seasonally tailored chemical-free skincare manufacturer formulations ideal for humid weather conditions.
Do you provide Ayurvedic raw materials for export?
Yes, as a reputed ayurvedic product manufacturer for export, we supply bulk ayurvedic raw materials supplier India for skincare, wellness, and therapeutic use to global clients.
Can you develop custom travel-size skincare kits for luxury hotels and spas ?
Absolutely. We specialize as a private label travel skincare kit manufacturer, delivering customized and premium travel kits under your hotel or spa’s brand.